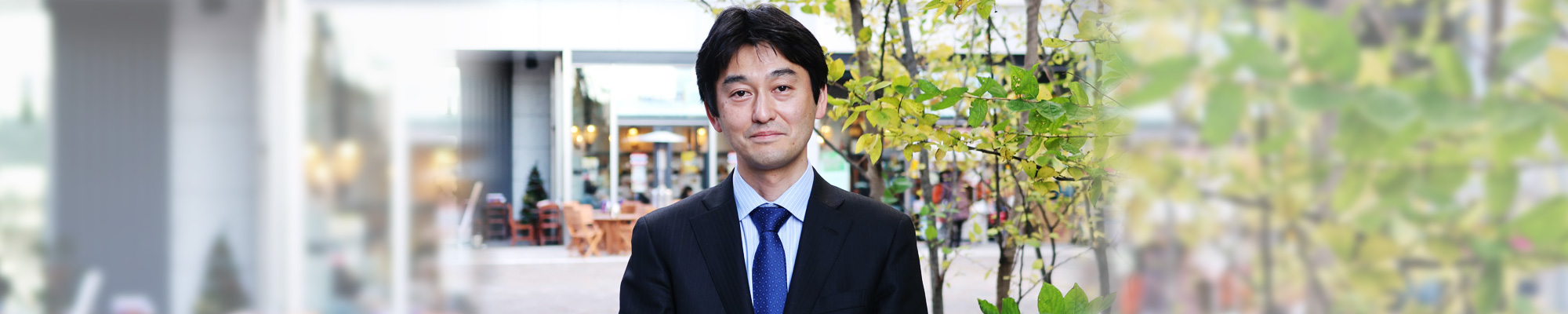
“Industry4.0” As a Break from Mass Production Manufacturing
Germany has been promoting government-backed efforts to digitalize its manufacturing industry. Known as “Industry4.0”, this initiative is gaining attention throughout the world, and even Japan is starting to see similar movement. It could have a major impact on manufacturing, even bringing about fundamental changes to how the industry operates.
Making factory operations more efficient with fewer personnel through automation
We now live in a world where physical objects are linked across networks and data can be readily exchanged and accumulated, and that means the time has come to transition to a more automated manufacturing structure. That, in a nutshell, is what “Industry4.0” is all about. This effort began in Germany starting in 2013, with the aim of making the manufacturing industry more competitive. NRI’s Takayuki Kobayashi, who has long provided consulting support to the manufacturing industry, had this to say.
“The idea is to get away from manufacturing that relies on the longstanding experience and intuition of human workers on-site, and instead to obtain data, implement whatever processing methods are optimal in a given case, and conduct predictive maintenance to prevent mechanical failures. This in turn will reduce dependence on people, and allow anyone to manufacture goods with flexibility and at the same level of quality.”
Why was there a government-backed effort in Germany to get involved in “Industry4.0”? There are two reasons for this, explains Kobayashi.
“One was to enhance competitiveness amid high costs. On the one hand, Germany has relatively high personnel costs compared to its eastern European neighbors, and it’s not easy to let workers go. That’s why it was necessary to adopt a more automated manufacturing model involving fewer personnel. The other reason was to raise factory efficiency. The operative concept here is to link all your factories operating in overseas locations as a network, treating them as one single factory, so to speak. For example, if you can’t manufacture something on time at your China factory, you can get the job done at your factory in Thailand. Doing that enables you to eliminate wastefulness, and thereby make your manufacturing process more efficient.”
A system for raising quality without depending on manpower
As a mature society faced with a manpower shortage from its dwindling birthrate and aging population, Japan is arguably in a similar situation to Germany’s. On top of that, manufacturing is a field where Japan shines. Japan could stand to learn a great deal from the efforts made in Germany.
“Japanese manufacturers also recognize the importance of digital data. In many ways, Japanese manufacturing is reliant on people. Although there’s a positive side to this, namely the way human resources are nurtured, given how the birthrate is declining and society is aging, it won’t be possible going forward to rely on people indefinitely. Plus, with automotive manufacturing for instance, the assembling of visible components requires training people, but things like semiconductor chips which are becoming increasingly miniaturized require the use of sensors and machinery if quality is to be improved. If that happens, product quality can be guaranteed no matter who does the manufacturing. A manufacturing system based on automation and standardization is something that Japan should also learn, I think.”
Achieving a manufacturing tailored to each individual customer
What sort of impact will the implementation of “Industry4.0” have on our society? Kobayashi sees it as an opportunity to break away from the mass production style of manufacturing that has existed up to now.
“In mature societies, the manufacturing of mass produced goods has slowly begun tapering off. Even in Japan, some household appliance makers have resorted to using foreign capital, and are even switching to producing items such as refrigerators and televisions overseas. As for what will happen next in these mature societies, we’re going to see them start producing goods that are customized to the needs of individual customers.”
For example, if a customer were to need refrigerators, the manufacturer would produce custom-made refrigerators tailored to the customer’s individual preferences, down to the last detail in terms of size, color, functions, etc.
“You might recall how PC manufacturers produce custom computers made-to-order, but the variation of customizability is really much wider than that. When a customer places an order online, the details are sent to the factory and brought to the production line, and upon completion the product gets delivered to the customer. This involves a transition away from the traditional value chain, which starts with development and finishes with shipment, toward a process that begins and ends with the customer. Together with a new value chain, this shift would inevitably bring about a change in both the mechanisms of business and the very organizational structures of companies.”
The emergence of CDOs (Chief Digital Officers) managing organizations based on digital technologies
With “Industry4.0”, increased networking allows for cross-sectional links to be formed not only in manufacturing systems, but in organizational structures that until now have been vertically compartmentalized. This means that corporate organizational structures as they currently exist will need to be redesigned. For corporations, this prospect would amount to a significant hurdle to overcome.
“Overall organizational design needs to be led by someone. With that said, who is to take on that role? Recently the position of CDO (Chief Digital Officer) has emerged overseas, and a trend has begun where entire corporate organizations are being managed and redesigned around digital technology. The role of people and the way personnel training is done are likely going to change significantly going forward. No longer will it suffice for developers merely to develop new products, or for manufacturing sites to focus solely on raising their efficiency. Everyone involved in manufacturing is constantly thinking about what kinds of service they should be providing to their customers—I think that’s the next stage for manufacturing.”
Profile
-
Noriyuki Kobayashi
* Organization names and job titles may differ from the current version.