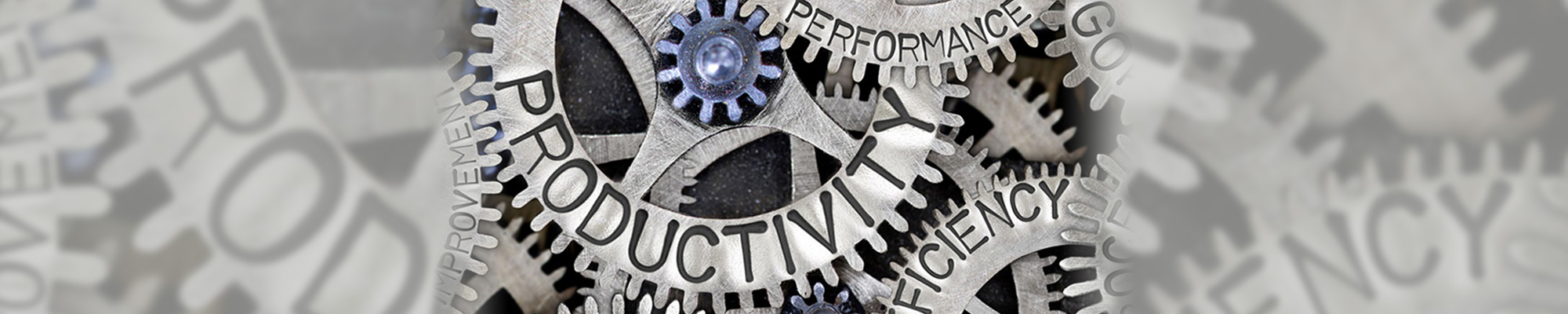
On productivity improvement
In recent years, the idea of productivity improvement has become increasingly common throughout the world. Japan’s labor productivity, however, has for many years been the lowest of the seven leading developed countries, and is now considered an issue on the national scale.
Until now, productivity has meant mainly, “how much cost can we save (cost productivity)?” In Japan, the spirit of continuous improvement in many companies (organizations) has meant their goal thus far has been the maximization of amounts. What is needed now, however, is a different perspective: “how much time can we save to try new things (improvement in added value)?” The important element in this kind of productivity is an improvement in the quality of time spent. “How and on what will we spend this time that we have secured, and how will we use it to create new value?
In this article, I will discuss productivity improvement, with examples from my work in system development.
Advancements in hardware and the cost productivity era
The 2000s saw a rapid shift from expensive host systems to low-priced, server-centered systems. With the dramatic advancements in hardware, it had become possible to replace host systems with hardware, and there was strong demand for reductions in IT costs. As a result, it became necessary to construct systems through short-term mass production (short-term, large-scale, and low-cost), a shift that dramatically altered the system development landscape.
Until then, systems were developed by engineers—craftsmen, almost—whose understanding of their own system was unique and irreplaceable. In other words, the systems were dependent upon the work of these specific engineers. The switch to short-term mass production led to a shortage of engineers, and as a countermeasure, many companies shifted entirely towards offshore development. At the time, however, “offshore” meant young engineers with little system development experience, and it was difficult to maintain quality. In order to do away with this dependence on engineers and their skills, there was a strong push towards system standardization. Standardization was possible because the technological elements of these systems were uniform, and it was not difficult to standardize and formalize the development process. After standardization, continuous improvement worked to further improve productivity. Productivity here, however, refers to how much cost is saved (cost productivity).
The digital age and the changing landscape
In recent years, however, there have been major changes in the system development landscape. First is the rise in costs at offshore production sites. With the economies of developing countries growing at an extremely rapid pace, there were predictions that costs in 2010 would be twice that of costs in the 2000s, ten years prior. The appreciation of the yen at one point, however, blinded many from the reality of this increase.
Short-term mass production, which had been the standard for the production of systems, saw its demand fall into decline, and the landscape shifted once again, this time, towards an opportunistic production system (only the necessary amount, at the necessary times). In-demand engineers went from being standardized, single-skill workers to flexible, multi-skill workers who could handle multiple steps of the development process.
Add to this circumstance the arrival of the digital age, exemplified by various technologies like IoT, AI, FinTech, and blockchain. The effects of digitalization have been deep and widespread, driving companies to create new business methods and business models, and have changed what we expect from IT in general.
Training engineers and improving added value through cutting-edge technologies
We have entered a new age and a new, digital world. In this world, the focus must be on how much time we can create, and how we can use this time to try new things (improvement in added value). It is important that we use this way of thinking towards a dramatic increase in productivity for our existing businesses, and work actively to invest in new business areas.
Productivity improvements in existing businesses must be conducted on a higher level than in the past, for us to be able to shift much of our resources to new business areas. In order to accomplish this, we must switch from our current production system, which utilizes many standardized, single-skill engineers, to a new one that utilizes a small number of elite, multi-skill engineers.
New business areas in the digital age require active adaptation to rapidly changing technologies, as well as the professional personnel to implement these technologies. There is a need for us to consolidate our organizations and engineers in accordance with their technological elements/skills, and increase the company’s level of professional skill as a whole.
The focus in productivity improvement is changing, from cost productivity to improvements in added value. In order to maximize performance, it is integral for companies to acquire and train multi-skill engineers who can utilize these new technologies, and be able to discern up-and-coming technologies (according to their spirit of innovation and maturation) and put them into practice.
Recently, a young employee said to me, “when I have free time, I don’t really know what to do.” Improvements in productivity create more time, but the use of this time is now increasingly dependent on individuals and their attitude. We have entered a new age—one where individual ability will be scrutinized more than ever.
NRI Research Paper Knowledge Creation and Integration November, 2017
Profile
-
Yasushi Kobara
* Organization names and job titles may differ from the current version.