社会における物流の重要度は高まり続けている。なかでも製造業や流通業にとっては商品自体の価値のみならず、短納期をはじめとした配送ニーズへの柔軟な対応が差別化要素の一つとなっている。
一方で慢性的な労働力不足や物流コストの高騰など、物流業界を取り巻く環境は厳しさを増している。2024年問題として取り上げられるドライバー不足だけでなく、物流倉庫で働く作業員の不足も問題となっている。
それらの解決策として、各社より物流倉庫で稼働する高性能な設備機器が提供されている。物流倉庫を運用する企業の多くはこれらを導入することで人員不足の問題を解消しつつ、さらなる効率化を図ろうとしている。しかし、限定的な効果にとどまる部分的な導入が多く、倉庫全体として見た場合には、DX(デジタルトランスフォーメーション)と呼ばれるほどの効果は出ていないのが実情である。
本稿では、全体として最適化された物流倉庫自動化を実現するため、その課題や進め方のポイントについて解説する。
先進デジタル技術の導入により大きく変わろうとしている物流倉庫
物流倉庫における作業の多くは、ローラーコンベアや台車などの単純なマテハン(マテリアルハンドリング)機器と人手によるアナログな作業が中心であり、これまではベテラン作業者の持つ経験や知見を頼りに成り立っていた。しかし、近年の人材不足に加え、荷主の要求の高度化などもあり、現場作業員によるアナログな対応だけでは急な計画変更や荷量の増加に対応できなくなってきている。
このような物流業界の問題を解決するために、設備機器メーカーからは人手をまったく介さない全自動マテハン機器や、自律的に学習して作業を最適化するAI搭載のマテハン機器など、従来の枠を超えた新しい設備機器が続々と登場してきている。代表的なものとしては、棚ごと商品を移動するGTP(Goods To Person:棚搬送型ロボット)、磁気テープやレール等のガイドが不要で自律的に動作する搬送ロボットであるAMR(Autonomous Mobile Robot:自立走行搬送ロボット)、事前設定や学習作業が不要で不定形物にも対応できるAIピッキングロボットなどが挙げられる(図1参照)。これらの機器の登場により、これまで人手が必要だった作業工程の中にもマテハン機器で代替できる領域が増え、ベテラン作業者と同等以上の生産性を期待できるようになった。
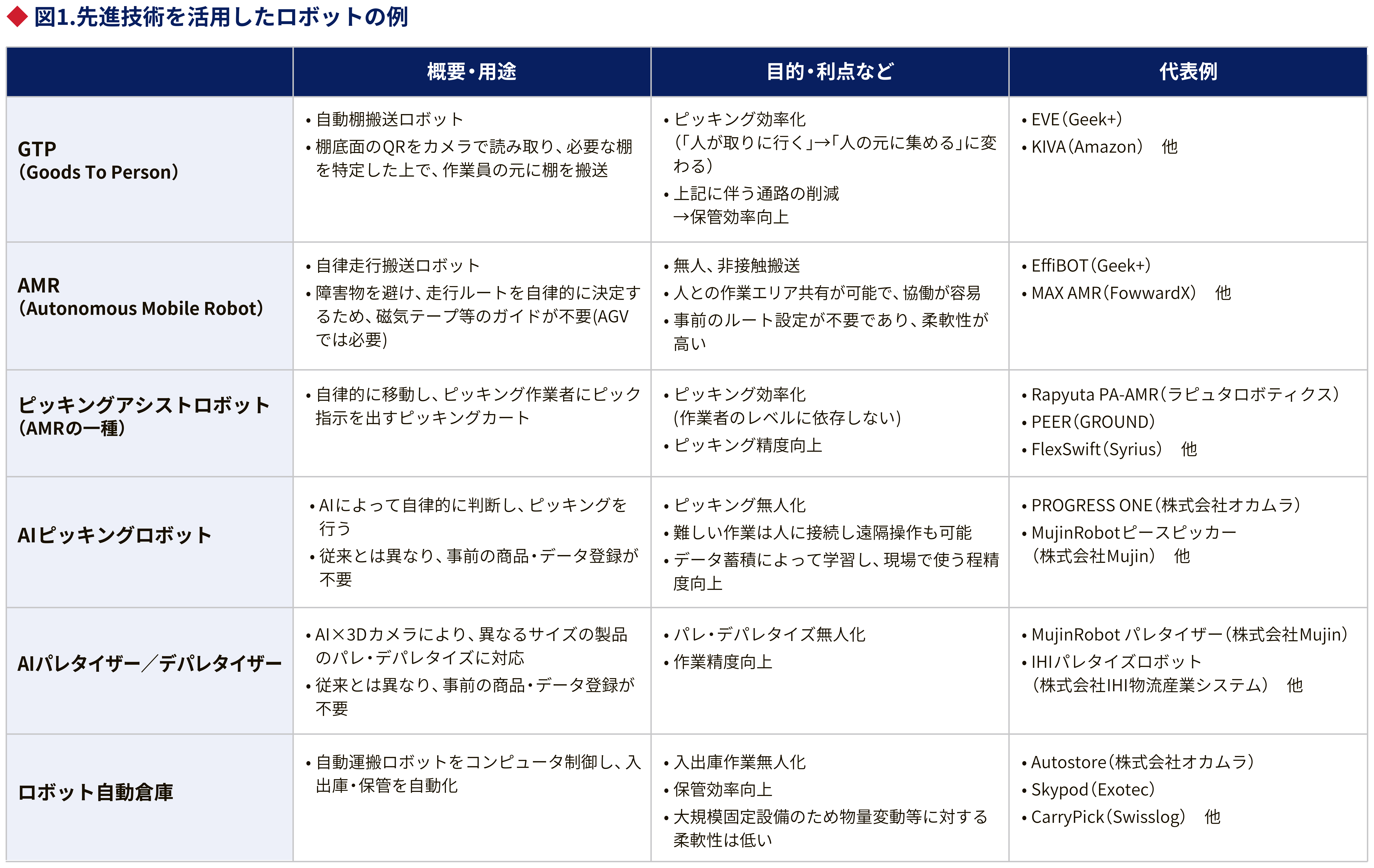
荷量の増大や、荷姿や商材の多様化といったビジネス環境の変化に対しても、このような設備機器を活用することで、作業員を新たに雇用したり再教育したりすることなく対応することが可能になってきている。
これら高度化された設備機器の特長は、情報システムと連係動作する点にある。動作実績をデジタルデータとして収集し、WES(Warehouse Execution System:倉庫運用管理システム)やWCS(Warehouse Control System:倉庫制御システム)等のソフトウェアを通じて、複数の設備機器を制御・連動させることも可能である。これらのソフトウェアを用いて倉庫全体の設備機器を協調動作させれば、倉庫全体を自動化させることができる。
例えば、ネットスーパー事業で有名な英国のOcado社は、巣ごもり需要を追い風にオンラインショッピングが拡大する中、品ぞろえを充実させて顧客へ迅速に提供することで他社に対して優位性を作り出している。これを実現するために構築した仕組みがOcado Smart Platform(以下、OSP)である。これは、情報システム(受発注、在庫管理、稼働シミュレーション、配車管理、最適ルート計算等)、自動倉庫、ピッキングロボット等から構成されており、注文からピッキング、袋詰め、配送までを自動で制御するためのプラットフォームである。具体的には、Webサイトに注文が入ると、注文情報をもとに倉庫から商品の入ったかごがピッキングエリアに自動的に搬送され、ピッキングロボットがかごから商品を選び出してバーコードスキャンした後、袋詰めを行う。これと並行して配車が実施され、ドライバーに配送指示および最適ルートを指示するといった一連の動作を行うのである(図2参照)。OSPでは、情報システムと各設備機器が連係することで、倉庫全体のみならず輸配送指示までを含めた自動化を実現している。OSPを開発したOcadoSolutionsは、日本でもネットスーパー事業の成長が著しいイオングループと提携しており、2021年に着工されたイオンフルフィルセンターにも同技術が導入される予定である。

物流倉庫自動化に失敗した例
高度化した設備機器を導入したものの、倉庫全体の視点が欠けていたために想定ほどの効果を出せずに失敗してしまった例も多い。
よく見られる例として、ボトルネックとなっていた工程を自動化してスループット(処理量)を向上させたものの、次工程の処理が詰まってしまい、倉庫全体としてはスループットがほとんど上がらなかったケースがある。例えば、商品を倉庫から仕分けラインに搬送して仕分けラインでピッキングする工程がある場合、前工程の搬送作業をいくら効率化しても後工程のロボットがそれに見合うスループットで仕分けできなければ、仕分けラインで待ちが生じてしまう。このケースでは、各工程の作業キャパシティやパフォーマンスを考慮するなど倉庫全体の視点での導入設計ができていなかったため、前後工程間でパフォーマンスが合わずに失敗してしまったのである。
また、複数ベンダーの製品の組み合わせで失敗したケースもある。昨今、多様な設備機器が多くの会社からリリースされているため、複数ベンダーの製品を組み合わせるケースも珍しくない。しかし、その多くはベンダー独自の仕様で作られているためインターフェースやロボットの制御の仕方に互換性がなく、異なるベンダーの製品を導入する場合はそれぞれを個別に制御する必要がある。その結果、全体としての整合が取れずに工程待ちを生み出す原因となってしまうのだ。
このように、設備機器の選択・導入においては倉庫全体の視点で検討しないと、部分最適な導入となってしまい失敗するリスクが高くなる。
倉庫全体の視点で現場のデータ化と自動化を設計することが必要
倉庫全体としての最適化を考える場合、複数の機器を一元的に管理できる情報システムが重要な役割を果たす。各工程の状況をデジタルデータとしてとらえることで、それぞれの工程の状況やスループットをリアルタイムかつ定量的に押さえることができるからだ。これらのデータをもとに、それぞれの工程における作業量と作業タイミングを指示することで、倉庫全体として最適化された無駄のないオペレーションを実現することができる。
例えばある倉庫では、ピッキングして搬送するまでの工程において、それぞれの工程における人の作業実績データと設備機器の作業実績データを一元管理している。これらを統合して分析することで、どの工程が遅れているのか、どの棚に在庫を配置すればよいのか、あとどれくらいのリソースを投下すべきか等が一目で分かるようになっている。この現場では、一元管理されたデータをもとに在庫配置やピッキング順、投入リソース等を常に調整することで、無駄のない効率的な作業を実現している。これまで、リソースの配置や作業順の調整等は熟練作業者の経験と勘にもとづき行われていたが、デジタルデータをリアルタイムに取得し分析することで、システムが自動的に最適な姿を提示することができるようになった。
このようなITを活用した倉庫内最適化を検討する場合は、以下の2点を整備する必要がある。
物流倉庫全体の状況をデジタルデータとして取得し、これらを一元管理する
まずは、それぞれの工程における稼働状況や実績データをデジタルデータとして取得し、倉庫内で一元的に管理できる状態にすることが必要である。単にそれぞれの設備機器や人手作業の実績がデータ化されているだけでなく、各データが特定のIDなどで連係可能な状態にする必要がある。
そのためには、作業者の動きや実績等を自動的に取得するセンシング技術や、設備機器から連係されるデータの整合性を考える必要がある。ただし、設備機器の仕様はベンダー間で異なるため、それぞれのインターフェースが異なるだけでなく、扱うデータの項目や単位等も異なることが多い。データの整合性がないため、設備機器の実績データや情報システムからの指示情報を集約したとしても統合して扱えないことが多い。このようなケースでは、WMS(Warehouse management Software:倉庫管理システム)レイヤでデータ統合を図ったり、WESなどのソフトウェアをWMSとWCSの間に配置したりするなどしてインターフェースの差異を吸収したうえで、それぞれの機器からのデータを統合していくことが望ましい。
リアルタイムな荷量や周辺工程の作業状況をもとに、それぞれの工程をコントロールする
次に、取得したデジタルデータをもとに、各工程の作業状況や実績をリアルタイムに把握し、各ラインに流す荷物量の制御や前後工程の作業内容、タイミング等をシステムで随時調整できることが重要になる。
キャンペーンなどによって扱う荷量の変動が非常に大きくなりがちなEC倉庫では、設置されている設備機器のキャパシティを荷量が超えてしまうことも珍しくない。ここでは、ラインを2つ設置し、それぞれのラインの荷量を情報システムで制御することでこれを解消している倉庫の例を紹介する。具体的には、この倉庫ではピッキングロボットとAMRを活用して定型の荷物に対する処理能力を最大化したラインと、ロボットで扱うことが難しい非定型荷物を人がピッキングして搬送するラインを用意している。普段は定型荷物は自動化ライン、非定型荷物は人手のラインで作業することで効率化を図っている。繁忙期には非定型荷物ラインに超過量分の定型荷物を流すとともに、一時的に人手リソースを増強することで設備機器のキャパシティを超えた荷量に対応させ、全体として膨大な荷量をさばけるように工夫している。どちらのラインへ荷物を流すべきかは、デジタル化された実績データや荷量データをもとに情報システムがコントロールしている。
このように、倉庫全体を無駄なく最適な状態で稼働させるためには、倉庫内の状況をデジタルデータとして常に把握できること、そしてこれらのデータの分析結果をもとに作業員や設備機器に一元的に指示できるよう倉庫を設計することが重要となる。
物流倉庫自動化の実行フェーズでは、全体整合性への留意が必要
物流倉庫の自動化を実際に進める際には、設備機器やソフトウェアを個別に導入するのではなく、全体の整合性に留意しながら進める必要がある。
ここでは、特に連係すべきデータ項目の策定方法、スケジュール、体制面での留意点について解説する。
設備・ソフトウェア間で連係するデータ項目は倉庫全体で同一の解釈の共有が必要
倉庫内の設備やソフトウェア間で連係するデータ項目は、最初にそれぞれのデータに対するメタ情報を定義し、倉庫全体で同一の解釈を共有することが重要である。上述したように各設備はベンダーによる独自仕様が多いため、同じ名前でも意味や解釈が異なるケースや、意味は同じでも桁数や形式等の型情報が異なるケースがある(図3参照)。これらの差異を初期段階で統一しておかないと、構築後のデータ連係時にデータの整合性が取れず、手戻りによる納期遅延や追加対応コスト発生の可能性が高くなる。統一する方法はさまざまだが(新項目を新たに定義して各ベンダーがその仕様を取り込む、一つのベンダーのメタ定義に寄せる等)、将来の機器更新や追加等を考慮すると、データ項目のメタ情報は誰もが理解できるように分かりやすく定義しておくことが望ましい。項目名の解釈が人によって違うことによるインターフェース仕様の誤解ミスを防ぐためだ。
これらの検討にはシステム的な目線からの知識が必要になる。自社内のシステム部門や外部の助けを借りながら進めるのも一つの策であろう。
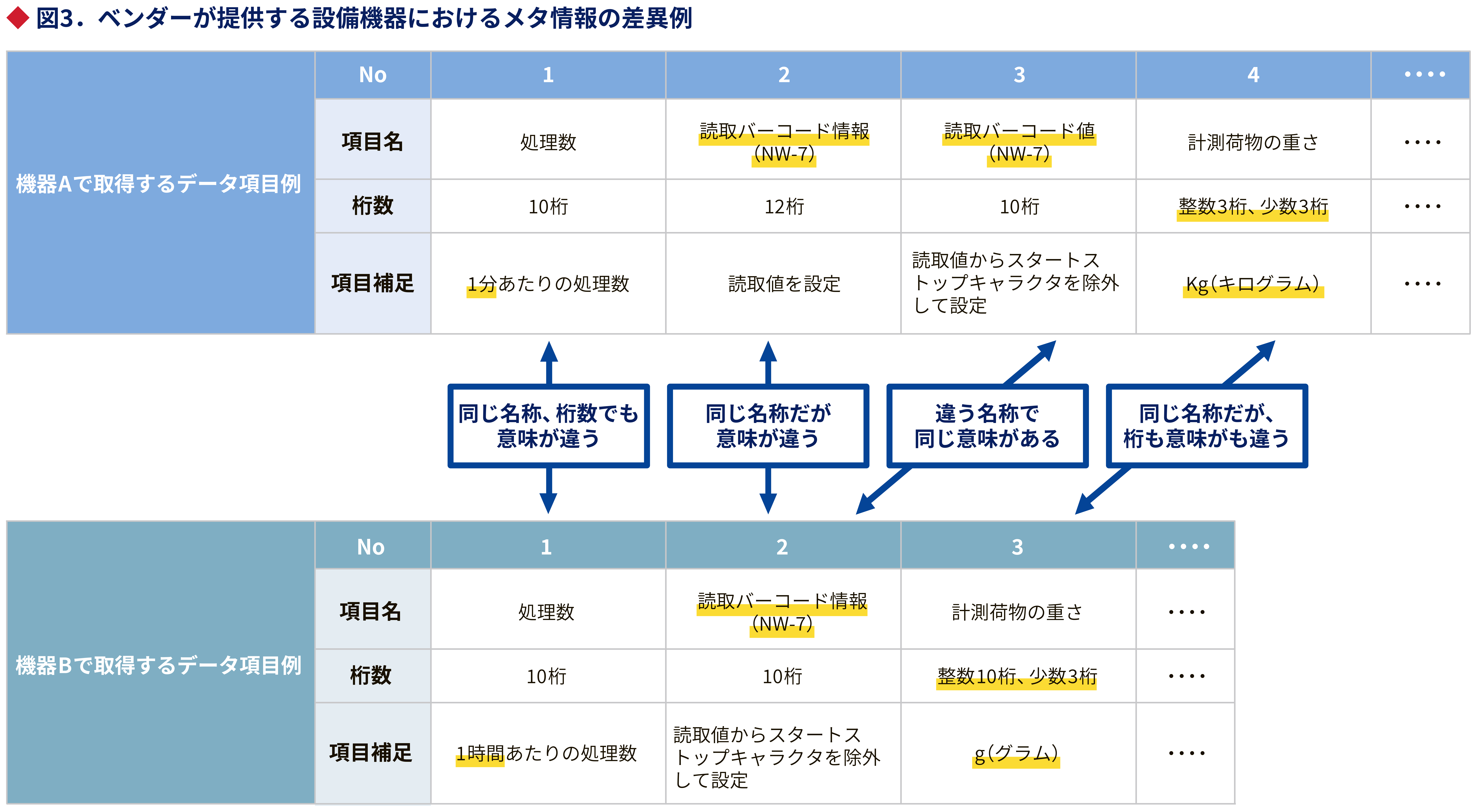
スケジュール策定、体制構築には、システム開発におけるテスト工程の考え方が有効
物流倉庫自動化を実現するためには、まず最初に倉庫全体が目指すべき姿を明らかにし、次に物流倉庫稼働日に向けて、機器選定、調達、構築といった各工程のスケジュールを策定する。機器調達後の構築工程では、倉庫内で稼働する設備やシステムといった単位で業者が見積もったスケジュールが策定され、利用する設備やシステムが多くなるほど、並行して進められる工事・開発が増えることに注意する必要がある。
ここでの留意点は、発注者側で品質を担保する必要があるということだ。複数の業者が関係する場合、各業者は自分の作業を優先するため、業者間同士で整合性が取れていないといったことが発生しがちだからだ。この点を意識せずに各業者に任せきりにした結果、稼働日になってはじめて設備・システム間の連係に大きな問題があることが発覚し、手戻りとなってしまうといった失敗事例も多い。
これらの問題の回避手段の一つとして、システム開発で取り入れられるテスト工程の考え方の導入がある。テスト工程の考え方では、「①業者の責任範囲や業者単体で確認すべき作業」「②隣接する業者間で確認すべき作業」「③倉庫全体での確認すべき作業」を工程として全体スケジュールの中に組み入れ、業者とあらかじめすり合わせる。この工程を組み入れて設備・システム間の連係品質を徐々に担保していくことで、問題発生時のリスクを最小限に抑えることが可能になる。そのためには業者との契約段階で、これらの工程を作業内容として組み入れておく必要がある。設備業者の場合、一般的な契約では自社の設備機器の倉庫への搬入、工事・構築、動作確認までといった例が多いため、システム開発的なアプローチを取り入れる際には、契約段階でその内容についての合意が必要である(図4参照)。
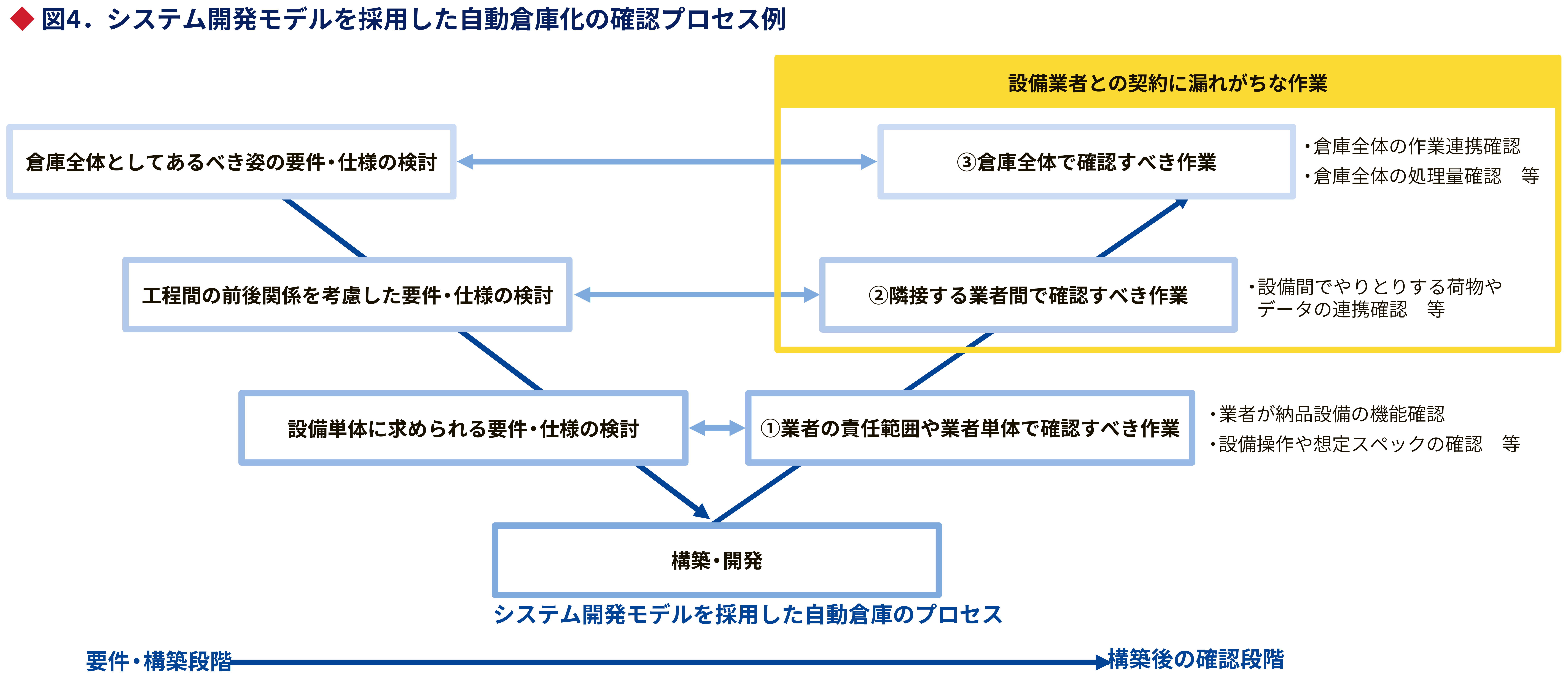
おわりに
物流倉庫自動化は、高性能な設備機器の導入という華やかな事例が目立つ一方、実際の導入に当たっては失敗する事例も多い。本稿で論じたポイントに留意して設備機器を導入していけば、Ocado社のような最先端の倉庫を実現することも夢ではない。
これから物流倉庫の自動化を検討されている企業の方、あるいはすでに実施中の企業の方に、ここで述べた内容が参考になればと思う。
執筆者情報
お問い合わせ
システムコンサルティングのご相談やお問い合わせはお気軽にこちらへ
-
株式会社野村総合研究所
システムコンサルティング事業本部
メールマガジン登録
DXに関する専門コンサルタントの最新レポートや、国内事例、技術解説、各種セミナー・イベント情報など、幅広い情報をお届けします。